Understanding What is Porosity in Welding: Causes and Solutions
The Scientific Research Behind Porosity: A Comprehensive Guide for Welders and Fabricators
Recognizing the complex systems behind porosity in welding is vital for welders and producers aiming for impressive workmanship. From the composition of the base products to the complexities of the welding process itself, a plethora of variables conspire to either worsen or reduce the existence of porosity.
Understanding Porosity in Welding
FIRST SENTENCE:
Exam of porosity in welding discloses vital insights into the honesty and high quality of the weld joint. Porosity, identified by the visibility of cavities or gaps within the weld steel, is a typical worry in welding processes. These spaces, if not effectively resolved, can compromise the architectural honesty and mechanical residential or commercial properties of the weld, bring about potential failings in the ended up item.
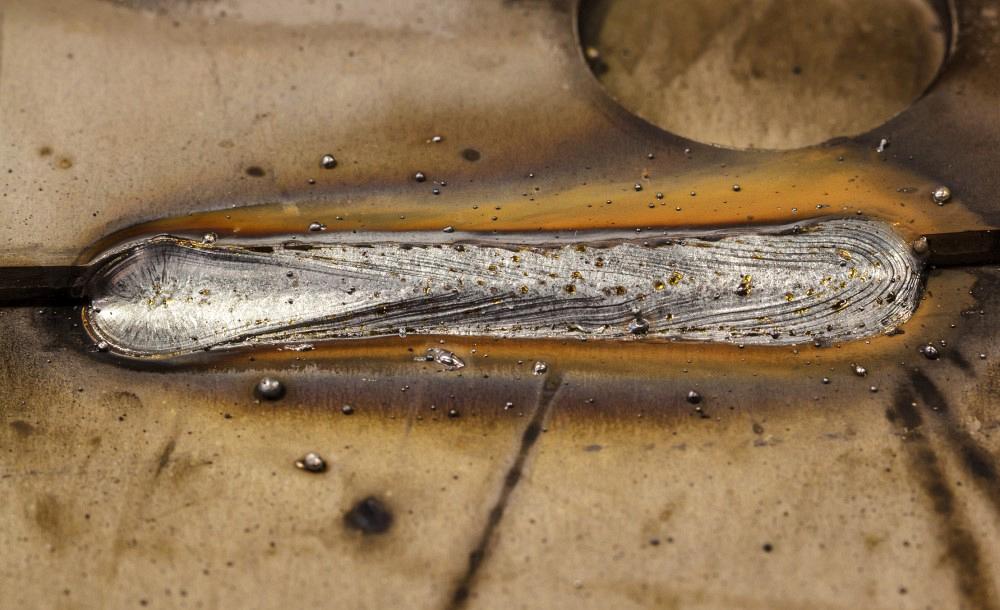
To detect and quantify porosity, non-destructive screening methods such as ultrasonic screening or X-ray inspection are usually employed. These strategies enable the identification of internal problems without compromising the honesty of the weld. By evaluating the size, form, and distribution of porosity within a weld, welders can make enlightened decisions to enhance their welding procedures and accomplish sounder weld joints.

Elements Influencing Porosity Development
The event of porosity in welding is affected by a myriad of aspects, varying from gas securing performance to the complexities of welding specification setups. Welding specifications, including voltage, current, travel rate, and electrode type, likewise influence porosity development. The welding technique employed, such as gas metal arc welding (GMAW) or protected metal arc welding (SMAW), can affect porosity formation due to variations in warmth circulation and gas coverage - What is Porosity.
Effects of Porosity on Weld Top Quality
The existence of porosity also compromises the weld's resistance to deterioration, as the caught air or gases within the gaps can respond with the surrounding atmosphere, leading to degradation over time. Furthermore, porosity can prevent the weld's capability to endure pressure or effect, more jeopardizing the overall high quality and dependability of the bonded framework. In essential applications such as aerospace, automobile, or structural building and constructions, where safety and security and durability are paramount, the harmful results of porosity on weld quality can have serious repercussions, emphasizing the significance of reducing porosity via proper welding methods and treatments.
Methods to Lessen Porosity
To improve the high quality of bonded joints and make sure structural stability, welders and makers use details methods targeted at reducing the formation of spaces and cavities within the product during the welding procedure. One effective approach to minimize porosity is to guarantee correct product preparation. This includes extensive cleansing of the base metal to get rid of any pollutants such as oil, oil, or wetness that can add to porosity formation. Additionally, utilizing the suitable welding specifications, such as the right voltage, current, and travel rate, is crucial in avoiding porosity. Preserving a constant arc length go to the website and angle throughout welding also helps in reducing the possibility of porosity.

In addition, choosing the best protecting gas and keeping appropriate gas flow prices are crucial in reducing porosity. Making use of the suitable welding strategy, such as back-stepping or utilizing a weaving movement, can additionally aid distribute warm uniformly and decrease the possibilities of porosity development. Making certain proper air flow in the welding setting to get rid of any web link prospective resources of contamination is essential for attaining porosity-free welds. By applying these techniques, welders can properly minimize porosity and produce premium welded joints.

Advanced Solutions for Porosity Control
Executing sophisticated technologies and cutting-edge techniques plays a pivotal role in attaining premium control over porosity in welding procedures. Furthermore, employing sophisticated welding methods such as pulsed MIG welding or customized ambience welding can additionally assist minimize porosity concerns.
One more innovative remedy entails the use of sophisticated welding devices. For example, making use of devices with built-in features like waveform control and innovative source of power can enhance weld high quality and lower porosity risks. Furthermore, the application of automated welding systems with exact control Learn More over parameters can substantially lessen porosity flaws.
In addition, incorporating innovative tracking and examination innovations such as real-time X-ray imaging or automated ultrasonic screening can help in spotting porosity early in the welding process, enabling immediate rehabilitative activities. Generally, incorporating these sophisticated services can considerably enhance porosity control and enhance the general high quality of bonded components.
Final Thought
To conclude, understanding the science behind porosity in welding is necessary for welders and makers to create high-quality welds. By determining the elements affecting porosity development and implementing strategies to reduce it, welders can improve the general weld top quality. Advanced solutions for porosity control can even more enhance the welding procedure and guarantee a solid and dependable weld. It is essential for welders to continuously educate themselves on porosity and implement best techniques to attain optimal outcomes.